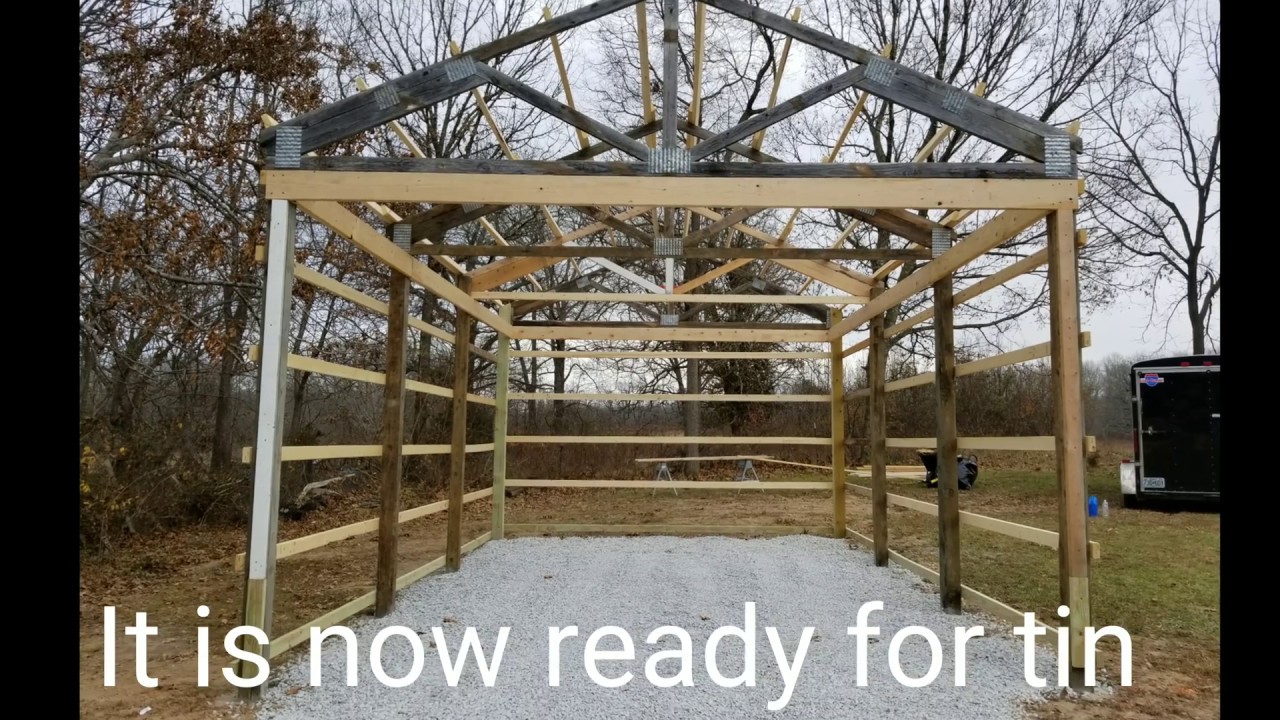
A pole barn, also known as a post-frame building, is a versatile and economical structure that can be a valuable addition to any farm. From housing livestock to storing equipment, these buildings offer practicality and affordability, making them a popular choice for DIY enthusiasts. This article will provide a comprehensive guide to constructing a DIY pole barn, covering everything from planning and design to the actual construction process.
1. Planning and Design:
a) Determine Your Needs:
Before embarking on your pole barn project, clearly define its purpose. Will it house livestock, store equipment, provide workshop space, or serve a combination of these functions? The intended use will dictate the size, layout, and features you need.
b) Site Selection:
Choose a level, well-drained site for your pole barn. Consider access for vehicles and potential future expansion. Ensure the site is free of underground utilities and obtains any necessary permits from your local authority.
c) Design and Size:
The size of your pole barn will be determined by your needs. Draw a detailed plan, including the dimensions, wall height, roof pitch, and any desired features like doors, windows, and ventilation. Consider the following:
Building Codes: Ensure your design complies with local building codes and regulations.
Foundation and Posts: Choose the appropriate foundation type and post size to support the structure's weight.
Roofing and Siding: Select materials that are durable and weather-resistant, while considering budget and aesthetic preferences.
Interior Features: Plan the interior layout, including partitions, electrical wiring, and plumbing if required.
2. Materials and Tools:
a) Materials:
Posts: Choose durable pressure-treated lumber, preferably 6x6 or 8x8, depending on the size and weight of your structure.
Foundation: Concrete piers, concrete footings, or gravel pads are common choices.
Framing Lumber: Utilize 2x4 or 2x6 lumber for the roof trusses, rafters, and wall sheathing.
Roofing: Select a material like metal roofing, asphalt shingles, or corrugated steel based on your budget and climate.
Siding: Choose from options like metal siding, wood siding, or vinyl siding, taking into account aesthetics and maintenance requirements.
Doors and Windows: Opt for sturdy, weather-resistant doors and windows that suit your needs.
Hardware: Include fasteners, nails, screws, hinges, and other necessary hardware.
b) Tools:
Power Drill: A powerful drill with a variety of bits for driving screws and drilling holes.
Circular Saw: For cutting lumber to size.
Tape Measure, Level, and Framing Square: Essential tools for accurate measurements and alignment.
Hammer: For driving nails and securing materials.
Post Hole Digger: For excavating holes for the posts.
Concrete Mixer: For mixing concrete for foundations.
Scaffolding: For safe access to higher areas.
Safety Gear: Always wear safety glasses, gloves, and appropriate footwear.
3. Construction Process:
a) Foundation Construction:
Prepare the Site: Level and compact the soil, then mark out the foundation layout.
Dig Post Holes: Use a post hole digger to excavate holes for each post, ensuring the correct depth and spacing.
Install Foundation: Choose the appropriate foundation type and install it according to the manufacturer's instructions. This could involve pouring concrete piers or footings, or setting gravel pads.
Secure Posts: Once the foundation is set, erect the posts and securely attach them to the foundation using bolts or concrete. Ensure the posts are plumb and level.
b) Framing and Sheathing:
Install Roof Trusses: If using prefabricated trusses, position them according to your design and secure them to the top plates of the posts. If building trusses yourself, carefully construct them using framing lumber and secure them with metal connectors.
Add Rafters: If you are not using trusses, install rafters at the appropriate spacing to support the roof.
Attach Wall Sheathing: Sheathe the walls with plywood or OSB panels, ensuring proper bracing and support.
Install Doors and Windows: After the framing and sheathing are complete, install the doors and windows, ensuring proper framing and weather sealing.
c) Roofing and Siding:
Install Roofing: Install the chosen roofing material according to the manufacturer's instructions, ensuring proper flashing and drainage.
Add Siding: Attach the siding to the walls, starting from the bottom and working up. Ensure proper overlap and secure attachment to the framing.
Install Gutters and Downspouts: Install gutters and downspouts to direct rainwater away from the building.
d) Interior Finishes and Utilities:
Install Insulation: If desired, install insulation between the wall studs and within the roof rafters.
Add Interior Finishes: Choose an appropriate finish for your interior walls and ceiling, such as drywall, plywood, or wood paneling.
Electrical and Plumbing: Install electrical wiring and plumbing as necessary, adhering to all local codes and regulations.
4. Final Steps and Maintenance:
a) Final Inspections and Cleanup:
Safety Checks: Thoroughly inspect the completed structure to ensure all components are securely fastened and there are no safety hazards.
Cleanup: Remove all debris and dispose of it properly.
b) Maintenance:
Roof Inspection: Regularly inspect the roof for damage, leaks, and debris accumulation.
Siding and Exterior: Clean the siding and exterior walls to prevent dirt and grime buildup.
Foundation and Posts: Monitor the foundation and posts for any signs of movement or damage.
General Repairs: Make timely repairs to any damage or wear and tear on the building.
5. Benefits of Building a DIY Pole Barn:
Cost Savings: Building your own pole barn can save you significant money compared to hiring a contractor.
Customization: You have complete control over the design and features of your building, allowing for a personalized solution.
Learning Experience: The process of building a pole barn offers valuable construction knowledge and practical skills.
Pride of Ownership: Completing a DIY pole barn project brings immense satisfaction and a sense of accomplishment.
Conclusion:
Constructing a DIY pole barn is a rewarding project that can provide a valuable asset to your farm. By carefully planning, gathering the right materials, and following the construction process outlined in this guide, you can successfully build a durable and functional structure that meets your specific needs. Remember to prioritize safety, adhere to local building codes, and take pride in your craftsmanship throughout the process. With a little effort and determination, you can achieve your dream of a DIY pole barn for your farm.
Sign up here with your email
ConversionConversion EmoticonEmoticon